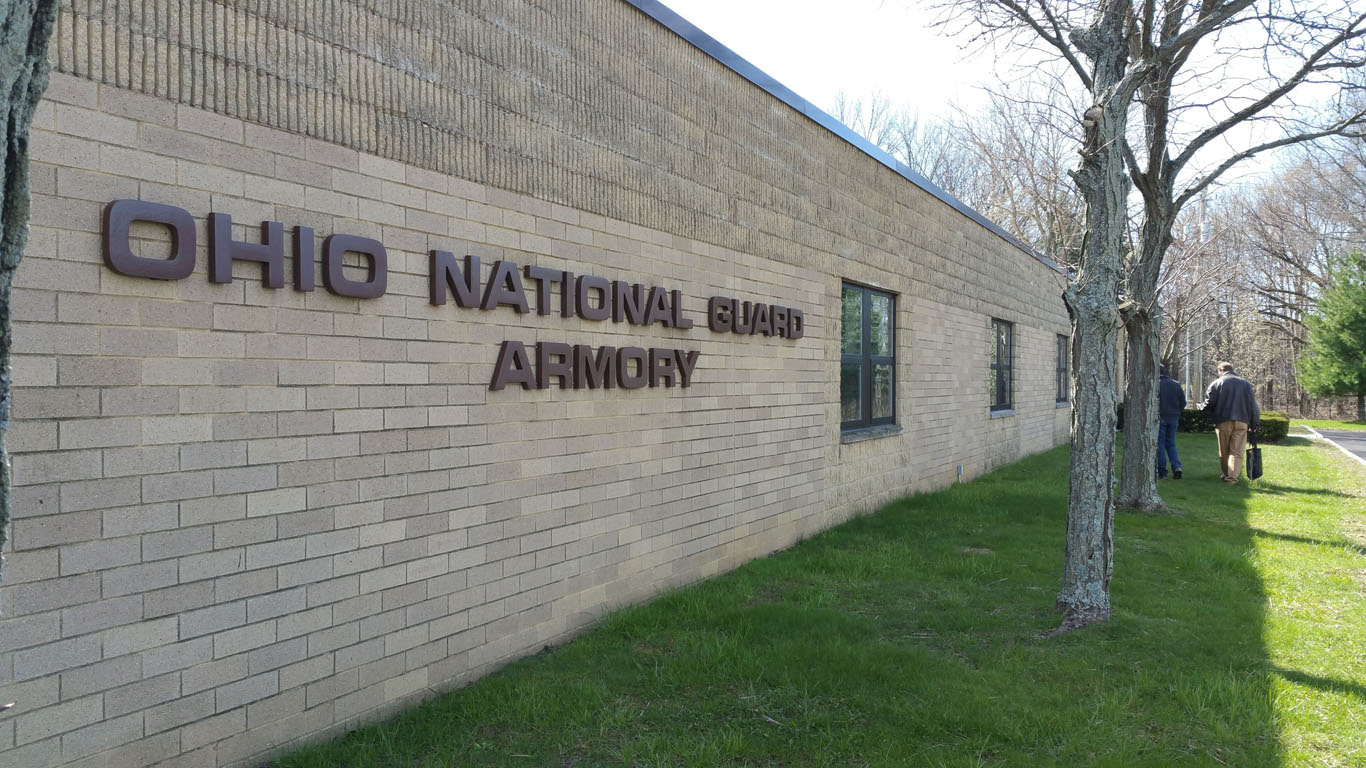
Ohio Adjutant General's Department
The National Guard owns and maintains over 3,000 armories across the nation serving over 360,000 members. These armories support local regiments of 600-1,000 soldiers in regular coordination and training activities to maintain readiness for emergency situations. In Ohio, the Adjutant General’s office leads the state’s nearly 17,000 guardsmen, housed mostly out of historic brick armories located throughout the state. While many armories are important installations in the community, being maintained by residents in some cases for over 100 years, longevity often requires care and upkeep, as displayed by the renovation projects shown here.
The Portsmouth Armory Renovation was an upgrade to the current Men’s and Women’s Restrooms. Serving Ohio’s National Guard as a regular training facility, it was paramount that the 1958 original restrooms be ungraded to meet current ADA guidelines and adhere to modern privacy standards, specifically with regard to the number of shower heads. The design intent provides a neutral color palette with highly durable materials to produce a long lasting, clean, modern look.
Like many of the armories throughout Ohio, the Youngstown Armory, was in need of significant repairs and upgrades to its systems in order to bring the facility up to code and provide significant energy savings. This project focused on improving the exterior masonry system, upgrading the HVAC and plumbing systems, and renovating the restrooms to meet ADA guidelines.
Unique to this armory was the use of fluted concrete masonry units. The Owner assumed they needed to tuckpoint 100% of the fluted CMU due to the significant amount of mortar deterioration, which is substantially more expensive than tuckpointing smooth faced masonry. Through our collaborative relationships with masonry contractors, we were able to reach out to several of them, to develop a detail that saved the Owner over 60% of their estimated masonry repair budget.
The Tarlton Armory Repair and Replacement consisted of three architectural components: Tuckpointing the CMU and brick exterior/repainting the CMU, replacing all existing exterior windows and doors to meet current energy requirements, and renovating the men’s and women’s restrooms to meet current ADA guidelines.
The building exterior would not hold paint. Our field inspection suggested that the problem was that the temperature dew point was being reached on the exterior of the non-insulated single wythe masonry wall. Our recommendation was to apply over a masonry primer, a two coat acrylic coating applied to a minimum dry film thickness of 3.7 mils per coat.
The Middletown Armory Renovation included tuckpointing and repairing of the exterior façade. Built in 1950, the Middletown Armory, like many of the armories built during that time, consists of an non-insulated CMU and brick face masonry façade. As a result, the façade requires constant maintenance in order to maximize energy savings, protect the overall structural integrity of the building, and increase the life expectancy of the facility.
We are proud of the fact that our Construction Document photographic representation of the building’s exterior walls, relative to the scope of the tuckpointing, resulted in zero change orders for a trade category fraught with cost overruns